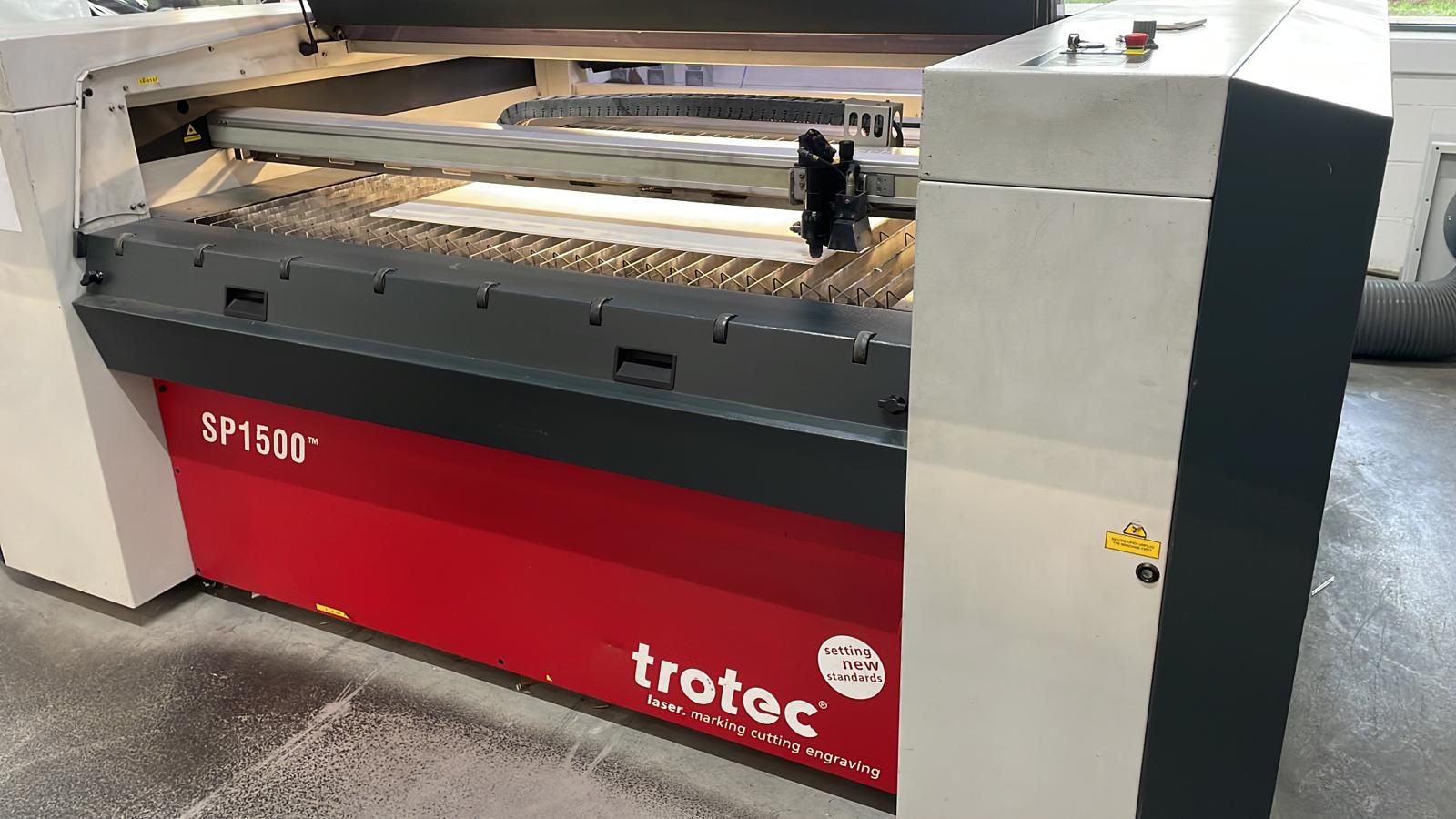
Founded in 1978 as Proctor Paper and Board, PPB Ltd has supplied customers with high-quality materials for over 40 years. Initially supplying paper and board, PPB has grown to provide a wide range of materials to the print and display industries, including acrylics, plastics and aluminium composite sheets.
A family business, PPB currently employs 50 staff, processing over 4500 orders monthly across two sites. With its history of supplying paper and other eco-friendly materials, sustainability continues to be a key focus for the business.
A growing business portfolio
At their headquarters in Leeds, PPB houses the majority of its stock materials. In 2016, the company further expanded its operations by purchasing plastic and acrylic specialist, NE Plastics. The acquisition of this business gave PPB an expanded product portfolio as well as a sizeable production site, alongside an established customer base in the area.
NE Plastics had been using a 3 m x 2m CNC router and Trotec SP1500 laser cutter at their Sidcup site, both of which are still used by PPB to this day, having been moved to a new Dartford location. The systems are operated by all employees and are used to fulfil customer orders across a range of applications.
With a wide range of equipment across the two sites and in line with their ethos for maintaining a sustainable business, PPB has taken steps to reduce their carbon footprint, including the addition of solar panels at their Leeds and Dartford sites and voltage optimisers to reduce excessive voltage.
Professional-grade laser cutting
The acquisition of the NE Plastics has been a driving force for PPB’s growth. There is a high demand for signage and materials in the local area and the team can effectively meet market requirements with high-quality laser-cut products from its Dartford location.
The laser cutter and CNC system have integrated seamlessly into PPB’s production, adding another string to their bow. The SP1500 is heavily used for production due to its ability to cut and engrave tight radii and intricate detail. The laser cutter’s contactless processing means that material usage is optimised and there is less chance of material damage. The PPB team process over 100 orders a day so they rely heavily on robust technology to meet customer demand. The SP1500 is in constant use for 8 hours a day.
In contrast to CNC processing, laser cutting acrylic significantly reduces production time for the team because flame polishing is not required. The SP1500’s 1500 x 1250 mm working area means the team can efficiently process large-format and small-scale jobs without compromising the quality of the finish.
Trotec supports all of its customers with ongoing service and support which is invaluable to businesses such as PPB Ltd.
Harry Proctor, Sales Manager at PPB Ltd, said:
“The Trotec laser is a professional-grade system that supports the production team in fulfilling a large number of orders and also ensures we are able to maintain quality standards. The level of detail that we can achieve with our SP1500, coupled with reduced production steps compared to the CNC allows us to deliver client work to the highest standard in a time-efficient manner.
“The Trotec laser system is an excellent addition to our production. It is professional-grade and allows us to supply consistent quality results.”